Commentary: Why zero-emission forklift rule is costly for farmers
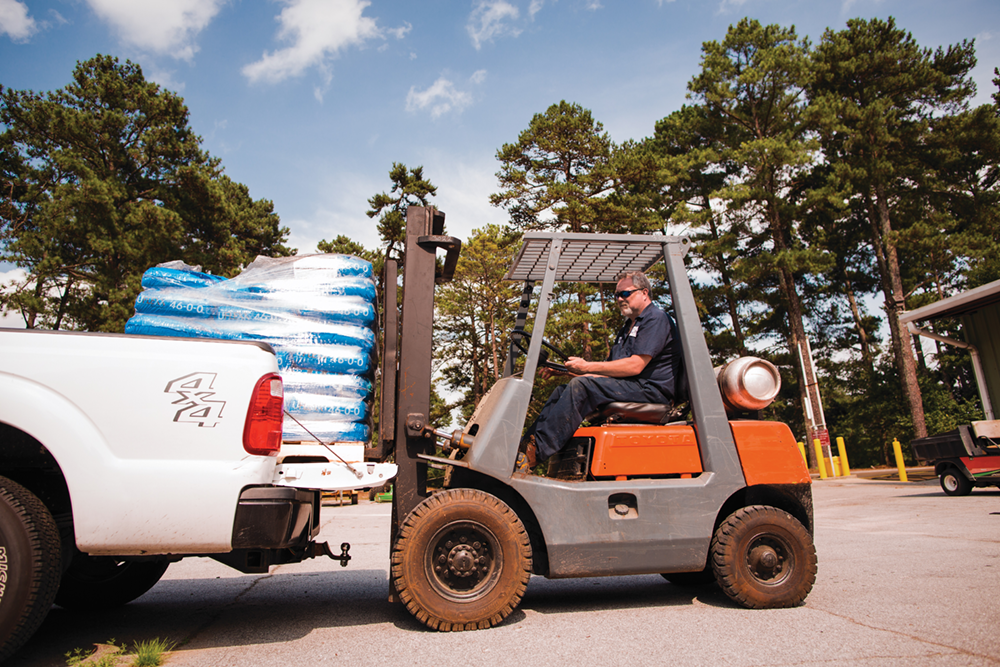
The California Air Resources Board is poised to adopt a new rule to eliminate internal combustion engine forklifts. The proposal would bring logistical burdens and added expenses for agriculture.
Photo/Western Propane Gas Association
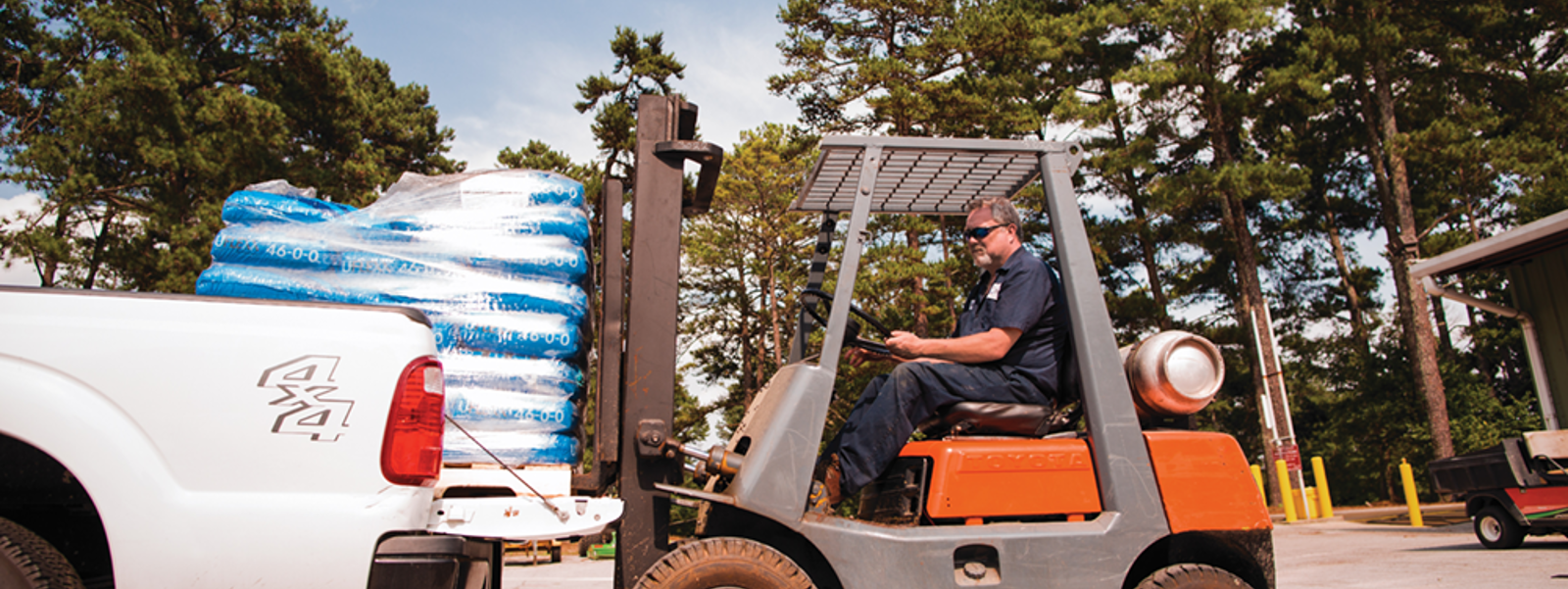
1.png)
By Colin Sueyres
The cost of farming and ranching operations—specifically moving hay, grain and produce—may be about to get a lot more expensive in our state.
That will be the outcome if the California Air Resources Board adopts its proposed rule to eliminate internal combustion engine, or ICE, forklifts across the state. The regulation, scheduled to be voted on June 27, would mandate that all Class IV cushion-tire combustion forklifts and the majority of Class V pneumatic-tire models be removed from existing fleets in favor of electric vehicles, namely forklifts powered by rechargeable batteries.
Forklifts are essential for many ranch and farm operations. Yet under the proposed rule, there are no exemptions for small fleets of forklifts moving goods within the agricultural sector. The rule would impact leased forklifts and force all owners and operators to purchase zero-emission forklifts by 2026—regardless of whether their current fleet of internal-combustion forklifts is still in good working condition.
The problem is exacerbated by the fact that there is not a 1:1 replacement, meaning farmers will have to purchase multiple electric forklifts to replace just one ICE forklift. This is because electric-vehicle forklifts require time to charge and cool and cannot run for 24 hours. Also, many EV forklifts cannot accommodate heavy loads like ICE forklifts can.
There will be associated infrastructure costs as electric forklifts need to be stored and charged indoors and new structures will need to be built, if not already available. Importantly, there are no exemptions for agricultural use or feasibility.
The Air Resources Board estimates that the number of impacted forklifts is approximately 95,000. However, an economic analysis by the Western Propane Gas Association found that the true number is closer to 220,000 ICE forklifts, more than half of all forklifts in the state.
The Western Propane analysis also found that, under the proposed new rule, costs to forklift owners and operators throughout the state could total up to $27 billion. These costs would include $10.2 billion for replacement of ICE forklifts even after factoring in salvage value and $4.6 billion in lost utilization costs for the premature retirement of currently functional ICE forklifts. In addition, charging station costs would exceed $6.3 billion to implement.
It is important to note that these costs do not factor in the cost of building power supply upgrades or infrastructure upgrades for the generation, transmission and delivery of electricity.
In numerous regulatory decisions across California’s history, the governmental body in charge has recognized that different regions or industries require different solutions. Unfortunately, the state Air Resource Board is moving forward with a one-size-fits-all rule that would set mandates without regard to the size of the business or the nature of the work.
Arguments regarding implementation from manufacturers, retailers, nonprofits and more have been ignored or rejected in favor of the board’s preferred technology solution.
Fortunately, there is a cheaper, more feasible and effective way to meet the state’s air-quality goals. Western Propane Gas Association has proposed an alternative pathway to compliance to ensure the state is meeting its greenhouse gas reduction goals while also protecting the goods-movement sector in critical industries across the state from untenable costs.
That alternative pathway would accomplish the following:
• Ensure that California has an accurate understanding of how forklifts are utilized within the state and how the rulemaking would affect real-world operations. Currently, there are no standardized databases within California to track actual forklift usage—leading CARB to significantly underestimate the true impact of the rule.
• Increase standards for future nitrogen oxide, or NOx, forklift emissions that recognize trends in capture technology and allow California to still meet its federally mandated emissions goals without a costly and ineffective one-size-fits-all technology mandate.
• Accelerate the phase-out of older, less efficient, higher emission pre-2011 forklifts to provide an immediate improvement in local air quality and reduce carbon intensity.
Unlike other industries such as the tech sector, which can outsource manufacturing or even relocate to more affordable states, the agricultural industry is here to stay. If you are concerned about how the California Air Resources Board rule will impact your farming operations, I encourage you to reach out to board members before the June vote.
I’m hopeful that, after hearing about real-world impacts of this regulation, the board is willing to come to the table and find a feasible and cost-effective way to meet our state’s ambitious air quality goals.
To review the analysis and see additional information regarding the impact of this rule across California, visit westernpga.org/forklift.
(Colin Sueyres is president and CEO of the Western Propane Gas Association. He can be reached at colin@westernpga.org.)